Discover the most up to date Developments in Metal Stamping for Accuracy Manufacturing
Discover the most up to date Developments in Metal Stamping for Accuracy Manufacturing
Blog Article
Advanced Techniques in Metal Stamping for Precision Manufacturing
As industries consistently demand finer tolerances and elaborate styles in their steel parts, the pursuit for innovative techniques in steel marking has heightened. From the application of advanced multi-stage stamping procedures to the integration of advanced automation technologies, the landscape of steel stamping is undergoing an extensive improvement.
Advanced Multi-Stage Stamping Procedures
Reviewing the intricacies of innovative multi-stage stamping processes discloses the advanced techniques employed in modern manufacturing methods. Metal Stamping. Multi-stage marking is a complicated procedure that involves numerous actions to change a level sheet of steel into a final stamped product. Using dynamic dies, where different operations are carried out at each phase of the marking procedure, permits high precision and performance in the manufacturing of complex steel parts
Throughout the first stages of multi-stage stamping, the flat steel sheet is fed into the stamping press, where a series of dies are utilized to reduce and shape the product. Subsequent phases entail extra developing, bending, and punching procedures to more fine-tune the component. Each stage is very carefully developed to build upon the previous one, resulting in the development of intricate geometries with limited resistances.
Advanced multi-stage marking processes need a high degree of experience and precision to ensure the quality and consistency of the stamped parts. By making use of advanced equipment and tooling, producers can create a variety of metal parts with efficiency and precision.
Precision Tooling Innovations
Precision tooling technologies have actually transformed the metal stamping industry, boosting efficiency and high quality in producing procedures. These advancements have substantially impacted the way metal elements are produced, causing higher precision and consistency in the end products. One crucial development is the advancement of computer mathematical control (CNC) innovation in tooling style and fabrication. CNC systems permit elaborate designs to be converted directly right into tooling, making sure precision and repeatability in the stamping process.
In addition, the integration of sensors and real-time tracking capacities in precision tooling has made it possible for manufacturers to find and resolve issues quickly, minimizing downtime and decreasing scrap rates. By integrating wise technology right into tooling, drivers can optimize specifications such as stress, rate, and placement during the marking procedure, resulting in boosted product quality and increased productivity.
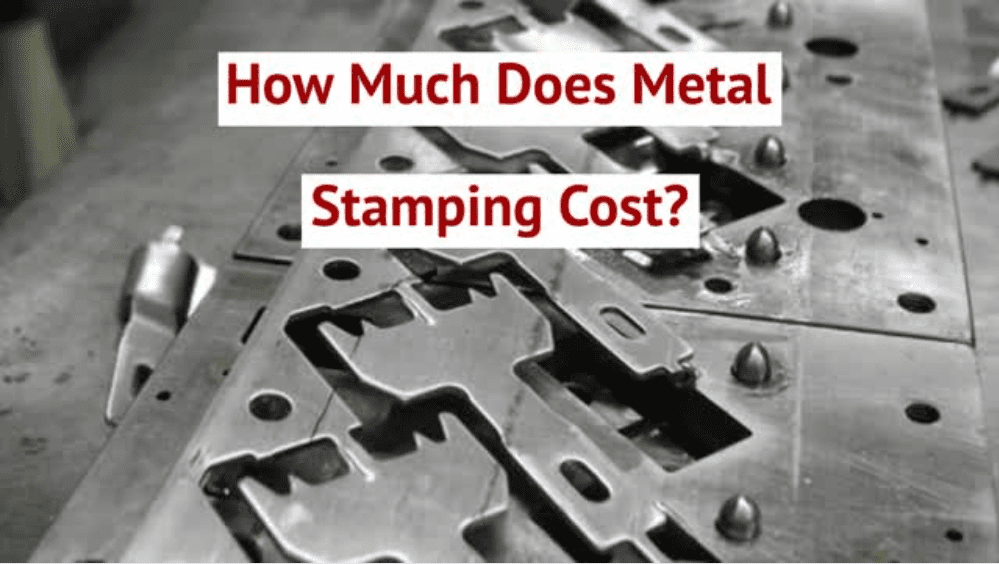
Automation in Steel Stamping
The development of precision tooling advancements in the metal marking market has actually paved the means for considerable improvements in automation, changing the manufacturing landscape towards boosted performance and productivity. Metal Stamping. Automation in metal marking involves the use of advanced machinery and robotics to do different jobs generally accomplished by human drivers. This change towards automation offers countless benefits, consisting of enhanced accuracy, faster production cycles, and reduced labor expenses
One trick aspect of automation in metal marking is the implementation of computer mathematical control (CNC) systems, which allow exact control over the stamping process. CNC technology enables the production of facility and detailed steel get rid of regular high quality. In addition, click for more automated systems can be configured to run continually, causing higher result rates and much shorter preparations.
In addition, automation enhances workplace safety by lowering hands-on handling of heavy materials and reducing the danger of mishaps (Metal Stamping). As producing sectors remain to embrace automation, the future of metal stamping holds excellent pledge for also greater effectiveness and advancement
High-Speed Stamping Methods
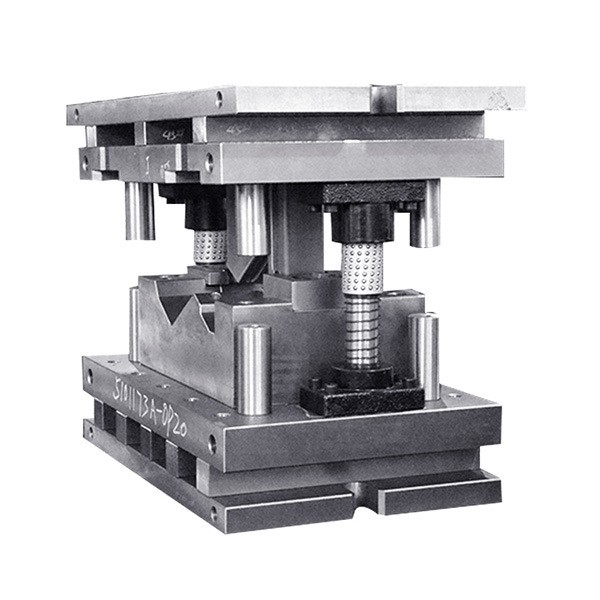
Among the main benefits of high-speed marking strategies is the ability to create a huge quantity of components in a shorter quantity of time compared to typical marking methods. This boosted performance not just permits producers to meet tight production target dates yet additionally enables expense savings via economies of scale. Additionally, high-speed marking can assist lower material waste by maximizing the product use during the stamping process.
Moreover, high-speed stamping methods usually incorporate ingenious features such as quick die modification systems and real-time surveillance abilities, better boosting the total effectiveness and adaptability of the steel stamping procedure. As innovation continues to development, high-speed marking is expected to play a crucial function in driving the future of accuracy manufacturing.
High Quality Control in Stamping Operations
Efficient quality assurance actions are important for making sure the dependability and consistency of metal stamping operations. Quality assurance in stamping procedures involves a series of methodical procedures focused on identifying and stopping defects in the produced elements. One essential facet of quality control in steel marking is using innovative evaluation strategies such as official statement optical evaluation systems and coordinate gauging machines (CMMs) to verify the measurements and resistances advice of stamped parts.
Furthermore, quality control measures in marking operations frequently include the implementation of analytical procedure control (SPC) techniques to keep track of the manufacturing procedure in real-time and make sure that it stays within acceptable limits. By analyzing data and identifying fads, manufacturers can proactively attend to any kind of discrepancies from the wanted high quality standards.
Moreover, quality assurance in steel stamping operations likewise includes thorough material testing to make certain that the raw materials utilized meet the called for requirements for the stamping procedure. This might include performing material firmness examinations, tensile strength tests, and dimensional evaluations to assure the high quality and stability of the stamped elements. Generally, carrying out durable quality assurance actions is essential for attaining top quality stamped parts consistently.
Verdict
Finally, progressed methods in steel marking play a vital function in accuracy production processes. Via multi-stage marking procedures, cutting-edge tooling services, automation, high-speed strategies, and strenuous quality assurance actions, makers can attain greater levels of accuracy and effectiveness in their operations. These developments in steel stamping modern technology have actually made it possible for companies to create complicated parts with limited resistances, inevitably bring about boosted product high quality and consumer fulfillment in the production industry.
Report this page